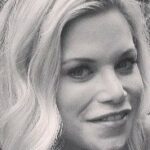
Work-in-process inventory – often known as WIP inventory – is pretty much its own field of expertise. This essential category covers everything from manufacturing to construction. Most importantly, it’s hugely important when you’re considering a company’s future growth potential.
Investors look at current WIP inventory to determine whether a company is a safe bet; lenders account for WIP inventory before approving loans. As for companies, they rely on low WIP inventory levels as they set out to plan their future growth strategies.
If you’re a bit lost about the meaning of WIP and its use for inventory control, you’re not alone! In our helpful guide below, you’ll learn more about the definition of WIP, how to calculate it properly, and some tips to use it to your benefit. Let’s dive in!
What is Work-in-Process Inventory?
Work-in-process inventory refers to the inventory created by raw materials that haven’t yet reached the finished goods stage. In other words, it includes the unfinished goods in the manufacturing process that are awaiting completion.
Any inventory that moves from raw materials and is manipulated by human or machine labor, but is not yet a complete product, is considered to be work-in-process inventory.
When you’re calculating the WIP inventory for your balance sheets, you will include manufacturing labor expenses and overhead costs in the final tally.
How to Calculate Work-in-Process Inventory
Work-in-process inventory calculations are designed to be an estimate. After all, detailing every aspect of WIP calculations could be tedious and more time-consuming than it’s worth!
In a manufacturing setting, WIP inventory calculations are calculated from basic raw materials plus human or machine labor costs and production overhead expenses. However, larger construction projects may also include wages, subcontractor costs, and more.
Most companies don’t account for potential negative scenarios, like spoilage, leftovers or scrap materials, operational downtime, or maintenance, repair, and operation (MRO) inventory.
Since so many things can go wrong during a production cycle, simple calculations are best when you want to get a solid estimate on WIP inventory costs.
But there’s one more step you’ll need to take before you start to calculate the WIP inventory in full — you need to figure out your beginning WIP inventory, manufacturing costs, and cost of goods manufactured (COGM).
Beginning WIP Inventory, Manufacturing Costs, and COGM
There are three elements you’ll need to define before you use a WIP inventory formula. Let’s take a look at each in detail.
The beginning WIP inventory is a type of carryover from the last accounting period‘s balance sheet. The current cycle’s beginning WIP inventory cost should be the exact same as the last cycle’s ending WIP inventory cost.
Manufacturing costs are a combined total of raw materials, human or machine labor expenses, and overhead costs.
The formula is:
Raw Materials + Human or Machine Labor Costs + Manufacturing Overhead Costs = Manufacturing Costs
The cost of finished goods (COGM) is the total cost of goods used in the making of a product. Furthermore, calculating the COGM is done by adding the total manufacturing costs to the beginning WIP inventory and subtracting the ending WIP inventory.
The formula is:
Total Manufacturing Costs + Beginning WIP Inventory – Ending WIP Inventory = COGM
Work-in-Process Inventory Formula
Once you know your beginning WIP inventory, manufacturing costs, and COGM you can start to use the WIP inventory formula. Here’s how you’ll need to do it!
Beginning WIP Inventory + Manufacturing Costs – Cost of Finished Goods = Ending WIP Inventory
If your head is spinning with all these figures, don’t worry!
As an example, let’s turn to a make-believe company, ABC Publishing. ABC Publishing starts the quarter with a work-in-process inventory of $25,000. This includes the glues, leather for bindings, and specialized paper for a particular book series.
Over the next six months, ABC Publishing incurs $100,000 in production costs to create the leather bindings, glue them, print, and deal with overhead for the machine. The total value of finished goods comes to $100,000.
Ending WIP Inventory = $25,000 + $100,000 – $100,000
Ending WIP Inventory = $25,000
The WIP inventory stays the same over the quarter. In general, a lower WIP inventory is best, but there are certain times in which a well-maintained WIP inventory is the optimal choice for a specific business model.
How to Optimize Work-in-Process Inventory Flow
Understanding the WIP inventory process is crucial for tracking and improving inventory control. A fluctuating WIP inventory can reveal signs of instability and it can even scare off potential investors. In contrast, a steady WIP inventory shows a trend of consistency.
However, some companies purposely opt to keep their WIP inventory a little high to maintain a buffer against shortages. Whether your WIP inventory is high or low, it’s still best to maintain your levels on a consistent basis.
WIP inventory can be difficult in the modern market. eCommerce has taken the world by storm. In trying to meet the needs of a global market, companies are struggling with inventory control, storage of goods, and allocation of materials.
Working directly with your supplier can help you to find out how their WIP inventory is being put to use; as well as what strategies you can implement to lower your own costs.
Optimizing your WIP inventory starts with making your supply chain more efficient. A partnership with a third-party logistics (3PL) provider might be just the answer you’ve been searching for!
Finding the Right Supplier
In eCommerce, many companies buy their products wholesale, so they often have no idea about the WIP inventory process. As a supplier, however, it’s important for you to know whether there are ways that your manufacturers can save money so that you can increase your savings!
To get a better understanding of the many ways you can produce your items, ask your manufacturer the following questions:
- Is there a bottleneck in transporting materials?
- Can distribution have better organization?
- Would partnering with a 3PL be helpful in fulfillment?
Your manufacturing company just might be growing faster than expected. Fast growth requires the ability to keep up with the market (and competitors!). A 3PL company could provide the resources you need to stabilize your supply chain!
How a 3PL Can Help
If you are a growing manufacturer, then it may be time to expand your storage. Raw materials and finished products can take up more space as your business grows, and there may not be enough time to build new warehouses.
A 3PL provides an array of solutions to help your business succeed, including distribution, procurement, and storage, as well as transport and fulfillment services.
Partnering with a 3PL like Print Bind Ship can make inventory management a breeze!
Partnering with a 3PL
So what’s the basic WIP meaning? It’s all of your inventory after the raw materials stage, but before the stage of the finished product. Whether you have raw materials that need to be stored or final products that are ready to be shipped, a 3PL can handle it all.
3PLs allocate space depending on a company’s specific needs. They can hold specialty materials like food or products. They also provide secure locations in the warehouse to hold volatile or sensitive products. When you partner with Print Bind Ship, you’ll enjoy full inventory tracking and auditing so that you can maintain and manage your stock while making the distribution of your products simple and streamlined!
Contact us today for a free consultation to see how we can make your inventory management easy!