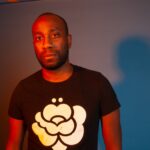
Making sure products get from the warehouse to customers as soon as they can is the goal of every business. But what do you do if your inventory system says something is in stock, but it’s clearly not? What do you do when your productivity has drastically decreased even though your orders have gone up? If your business is facing trouble that you can’t pinpoint in your fulfillment lane it’s time for you to conduct a warehouse audit.
What is a Fulfillment or Warehouse Audit?
A fulfillment audit is the process used to reduce hours worked while still improving a warehouse’s efficiency.
Benefits of Fulfillment and Warehouse Audits
When done correctly a fulfillment audit will improve your company’s processes. The problems you uncover in your warehouse audit can remove bottlenecking issues and improve morale, which will increase productivity and help your company’s turnover rate. Warehouse audits can improve processes that could be costing you money or your reputation.
Improve Efficiency
The core purpose of a fulfillment audit is to find your warehouse’s weaknesses and improve your company’s processes. Productivity is generally measured by orders picked per hour. During your warehouse audit, you’ll check your logistical layouts, storage and handling equipment and internal housekeeping practices. Fixing inefficiencies in your material flow and inventory management systems allows your warehouse to pick and pack with few mistakes and less lead time.
Obtain Data
To correctly perform a warehouse audit you must first obtain the correct data. By gathering information on employee accuracy, turnover, on-time delivery, customer complaints, organizational surveys and quality assurance (QA) numbers, you can see a nonbiased, top-down view of how your organization can improve its warehouse operations.
Find and Eliminate Unnecessary Expenses
As with conducting any audit, redundancies may be found, but when conducting a warehouse audit you may find these redundancies can cost you time and money. Having the possibility of redundancies in equipment and redundancies in processes can cost you valuable time and costly manhours.
Deprecated practices can be brought on by old processes or new equipment. Conducting a fulfillment audit will help you remove these and other unnecessary expenses.
Warehouse Audit Checklist
Now that you know the way, in the next section, we’ll show you how to do a fulfillment order warehouse and some of the areas that should be at the top of your checklist.
Define Audit Goals
When doing a warehouse audit it’s important that you don’t move the goalpost and that you understand the key performance indicators (KPIs) you’re trying to improve or learn more about. With all of the data you’ve collected, you can make actionable choices to further streamline your warehouse
Count Physical Inventory
One of the biggest problems with warehousing, other than a non logistic-based warehouse, is overstock. Having products you can’t get rid of is a nuisance of its own, and having to warehouse those palettes is worse. Counting your physical inventory is a great way to audit your inventory management system. Finding discrepancies between your count and the computer’s can be a sign that there’s a glitch in the system or in your company’s process.
Watch Over Warehouse Operations
Physically walking through the processes of your warehouse is an integral part of a fulfillment audit. When you walk through your live warehouse, you get to see your employees’ pace — even if they end up being a little faster with you on the floor, you’ll be able to see how they work and have a chance to ask why certain operations may seem to overextend.
Talk To Employees
Even if you’re in the trenches with your team, you can have blind spots. Talking with your team leaders will give you a perspective on where they see problem areas. Meeting with your warehouse team will help you figure out ways to make your fulfillment process more efficient.
Evaluate Inventory Data
After looking at the data you’ve gathered from your inventory management system and comparing it with your output, frequency of need and storage requirements, you can make better pick-and-pack decisions.
Review Audit Results
At the end of your warehouse audit, take all of your findings seriously to make adequate changes to your business to make it more profitable.
Offload and Outsource to the Pros
Though doing a full and thorough review of your warehouse is recommended for any business that uses a pick-and-pack shipment style, you don’t have to do it alone. Print Bind Ship not only has the full capabilities of any major third-party logistics (3PL) provider, but our warehouses are also always optimized for your shipments to go out within 24 hours of processing.
FAQ
A warehouse audit should include processes, inventory management, employee productivity, organization redundancies, storage and handling procedures, general housekeeping, security, product flow and logistics, as well as areas of improvement and failure.
Make sure all of your KPIs are being captured in your data points.
You should look for key points of growth and repair in your warehouse audit.